Fraunhofer Institute IOSB and SBG Systems Collaboration
Fraunhofer Institute is a renowned German research organization, has been a pioneer of innovation in a wide range of scientific domains.
“Autonomous large-scale robots are set to revolutionize the construction industry soon, transforming efficiency and innovation.” | Florian OLLIER, Head of Marketing at SBG Systems
Fraunhofer institute, a renowned German research organization, has been a pioneer of innovation in a wide range of scientific domains. Within its extensive network of 76 institutes, the Fraunhofer Institute of Optronics, System Technologies and Image Exploitation IOSB stands out for its groundbreaking work in autonomous mobile robotic systems.
This case study explores the collaboration between Fraunhofer IOSB and SBG Systems, focusing on the integration of our inertial sensors into autonomous construction vehicles.
Reshaping construction technology
Autonomous systems have become indispensable for tasks that are dangerous, difficult, or monotonous for humans.
Fraunhofer IOSB’s Autonomous Robotic Systems research group specializes in the development of autonomous construction vehicles, ranging from excavators for unstructured environments to Unimogs that pull a dump truck to remove the soil away from the construction site.
Autonomous vehicles must understand their environment and create a 3-D map to determine their location. They use data from sensors to figure out how to move around in their environment.
A proud collaboration
To achieve true autonomy in construction vehicles, accurate and reliable sensors are crucial. These sensors must provide real-time data for environment perception, mapping, and navigation.
Fraunhofer IOSB needed a supplier that could deliver high-performance inertial sensors to enhance the capabilities of their autonomous construction vehicles.
We are proud to collaborate with the esteemed Fraunhofer Institute, renowned for its innovation. Fraunhofer IOSB has used several of our products on various platforms.
Implementation
One notable application involves the integration of our Ekinox inertial sensor into an autonomous excavator capable of removing soil.
Ekinox played a key role in capturing the vehicle’s motion and orientation data, enabling precise mapping of the environment in real time.
This data, combined with advanced algorithms developed by Fraunhofer researchers, enabled precise perception, mapping, and navigation.
Results
- Autonomous excavation/ Autonomous soil removal: The excavator equipped with SBG Systems’ Ekinox Micro achieved a high level of autonomy in soil removal tasks. The inertial sensor’s accuracy and reliability contributed to the vehicle’s ability to operate independently in unstructured environments.
- Salvaging barrels: The autonomous excavator demonstrated versatility by extending its capabilities to salvage barrels. It was able to perform various tasks within its area of operation.
- Unimog operations: Fraunhofer IOSB is currently in the process of converting the Unimog into a robot towing a dump trailer to transport soil away from the construction site. SBG Systems’ inertial sensors power the autonomy pipeline, expected to enhance the operation’s efficiency and safety.
In few words
Fraunhofer IOSB and SBG Systems’ partnership demonstrates how advanced sensor technology and innovative research can achieve significant advancements.
Integrating advanced IMUs to self-driving construction vehicles not only improves what machines can do today but also opens the door for exciting future changes in autonomous robotics.
Fraunhofer IOSB and SBG Systems collaborate to push the boundaries of autonomous technology.
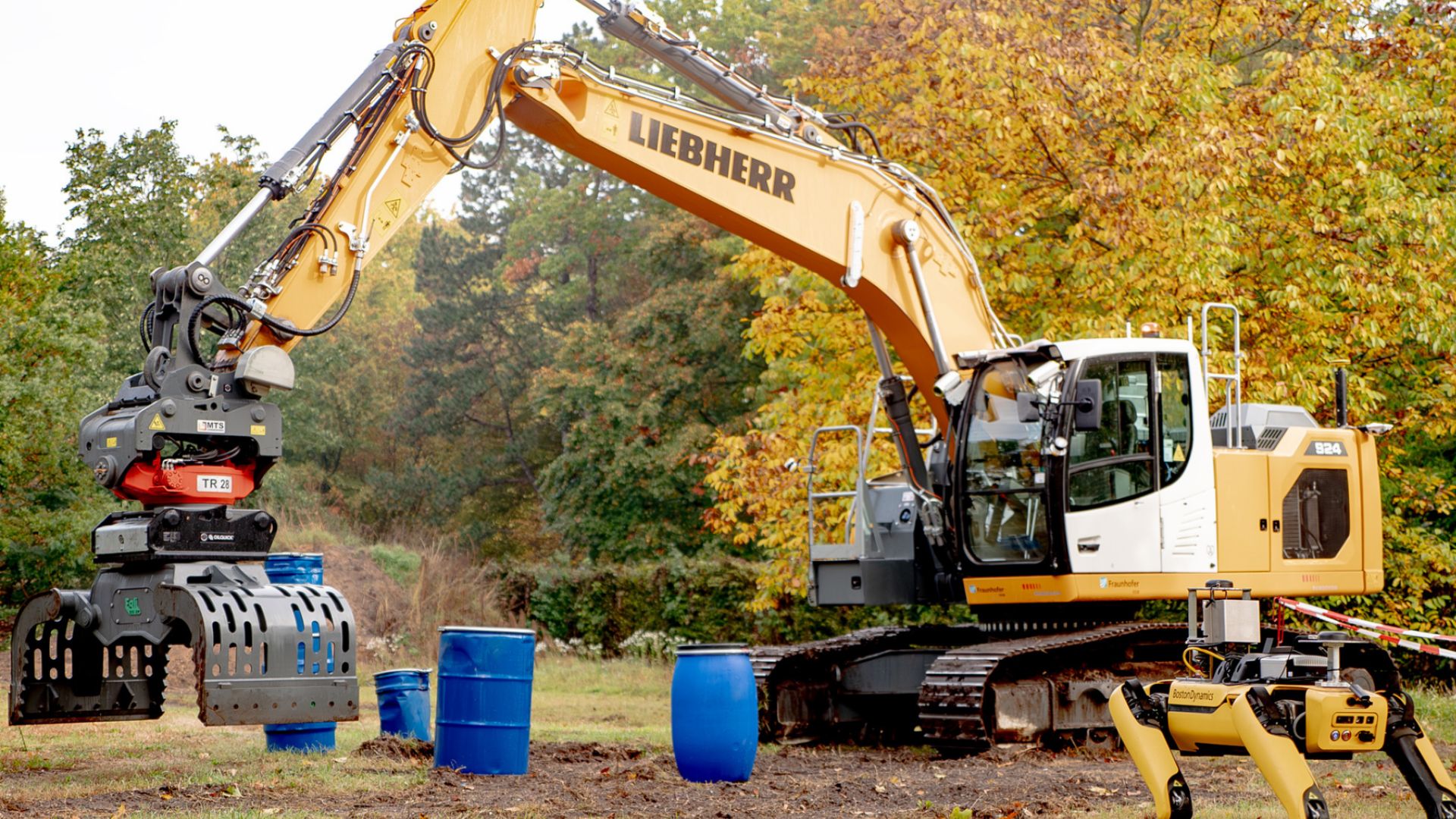
Ekinox Micro
Ekinox Micro combines a high-performance MEMS inertial sensor with quad-constellation, multi- frequency dual-antenna GNSS receiver to provide unmatched accuracy even in the most challenging applications.
Designed to operate in the harshest conditions, Ekinox Micro is qualified with military standard, making it the ideal choice for any mission critical application.
Ask a quotation for Ekinox Micro
Do you have questions?
Welcome to our FAQ section! Here, you’ll find answers to the most common questions about the applications we showcase. If you don’t find what you’re looking for, feel free to contact us directly!
What is a payload?
A payload refers to any equipment, device, or material that a vehicle (drone, vessel …) carries to perform its intended purpose beyond the basic functions. The payload is separate from the components required for the vehicle operation, such as its motors, battery, and frame.
Examples of Payloads:
- Cameras: high-resolution cameras, thermal imaging cameras…
- Sensors: LiDAR, hyperspectral sensors, chemical sensors…
- Communication equipment: radios, signal repeaters…
- Scientific instruments: weather sensors, air samplers…
- Other specialized equipment
What is GNSS post-processing?
GNSS post-processing, or PPK, is an approach where the raw GNSS data measurements logged on a GNSS receiver are processed after the data acquisition activity. They can be combined with other sources of GNSS measurements to provide the most complete and accurate kinematic trajectory for that GNSS receiver, even in the most challenging environments.
These other sources can be local GNSS base station at or near the data acquisition project, or existing continuously operating reference stations (CORS) typically offered by governmental agencies and/or commercial CORS network providers.
A Post-Processing Kinematic (PPK) software can make use of freely available GNSS satellite orbit and clock information, to help further improve the accuracy. PPK allow for precise determination of a local GNSS base station’s location in an absolute global coordinate reference frame datum, which is used.
PPK software can also support complex transformations between different coordinate reference frames in support of engineering projects.
In other words, it gives access to corrections, enhances the project’s accuracy, and can even repair data losses or errors during the survey or installation after the mission.
What is GNSS vs GPS?
GNSS stands for Global Navigation Satellite System and GPS for Global Positioning System. These terms are often used interchangeably, but they refer to different concepts within satellite-based navigation systems.
GNSS is a collective term for all satellite navigation systems, while GPS refers specifically to the U.S. system. It includes multiple systems that provide more comprehensive global coverage, while GPS is just one of those systems.
You get improved accuracy and reliability with GNSS, by integrating data from multiple systems, whereas GPS alone might have limitations depending on satellite availability and environmental conditions.
GNSS represents the broader category of satellite navigation systems, including GPS and other systems, while GPS is a specific GNSS developed by the United States.
Does INS accept inputs from external aiding sensors?
Inertial Navigation Systems from our company accept inputs from external aiding sensors, such as air data sensors, magnetometers, Odometers, DVL and other.
This integration makes the INS highly versatile and reliable, especially in GNSS-denied environments.
These external sensors enhance the overall performance and accuracy of the INS by providing complementary data.
What is the difference between IMU and INS?
The difference between an Inertial Measurement Unit (IMU) and an Inertial Navigation System (INS) lies in their functionality and complexity.
An IMU (inertial measuring unit) provides raw data on the vehicle’s linear acceleration and angular velocity, measured by accelerometers and gyroscopes. It supplies information on roll, pitch, yaw, and motion, but does not compute position or navigation data. The IMU is specifically designed to relay essential data about movement and orientation for external processing to determine position or velocity.
On the other hand, an INS (inertial navigation system) combines IMU data with advanced algorithms to calculate a vehicle’s position, velocity, and orientation over time. It incorporates navigation algorithms like Kalman filtering for sensor fusion and integration. An INS supplies real-time navigation data, including position, velocity, and orientation, without relying on external positioning systems like GNSS.
This navigation system is typically utilized in applications that require comprehensive navigation solutions, particularly in GNSS-denied environments, such as military UAVs, ships, and submarines.