Understanding active heave compensation
The core of AHC technology relies on the integration of various components, including motion sensors, hydraulic systems, and control algorithms. Motion sensors, typically accelerometers and gyroscopes, continuously monitor the vessel’s movements and detect any heave caused by ocean waves.
The data collected is transmitted to a control system, which processes the information and determines the necessary adjustments to the lifting equipment’s position.
The hydraulic system then actuates the compensator, which dynamically adjusts the height of the load being lifted, counteracting the vessel’s motion. This ensures that the load remains stable and at the desired depth, regardless of the vessel’s vertical movements. By employing AHC, operators can maintain precise control over equipment and minimize the risk of accidents and damage during marine operations.
Discover our solutions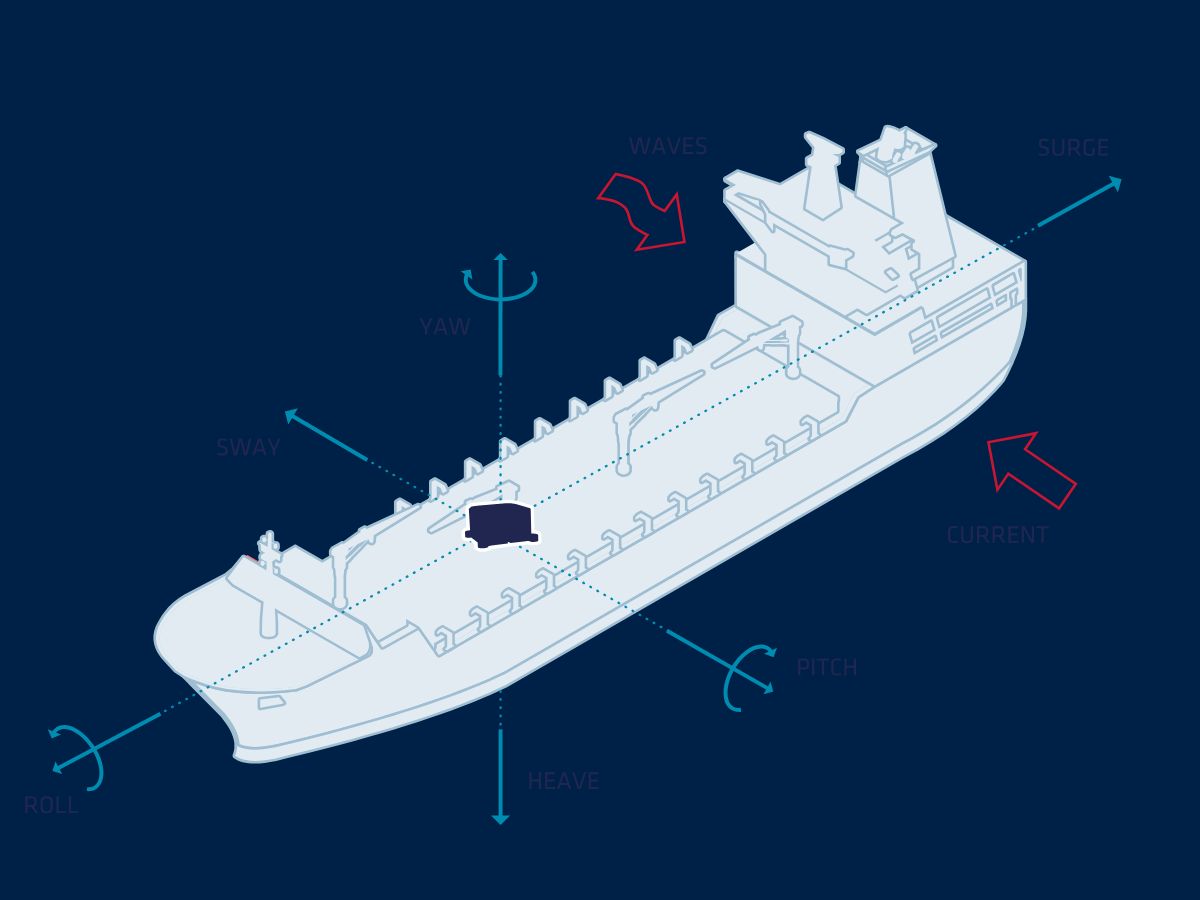
Benefits of our sensors for AHC systems
Embedding our sensors with an Active Heave Compensation system offers numerous advantages to maritime operations. By maintaining a stable working platform, AHC motion sensors reduce the risk of accidents and injuries during operations, protecting personnel and equipment. Enhanced safety and efficiency lead to lower operational costs and reduced downtime, resulting in more cost-efficient operations that save time and money.
Active Heave Compensation systems can be integrated into various marine vessels and equipment, making them versatile solutions for different applications.
Download our brochure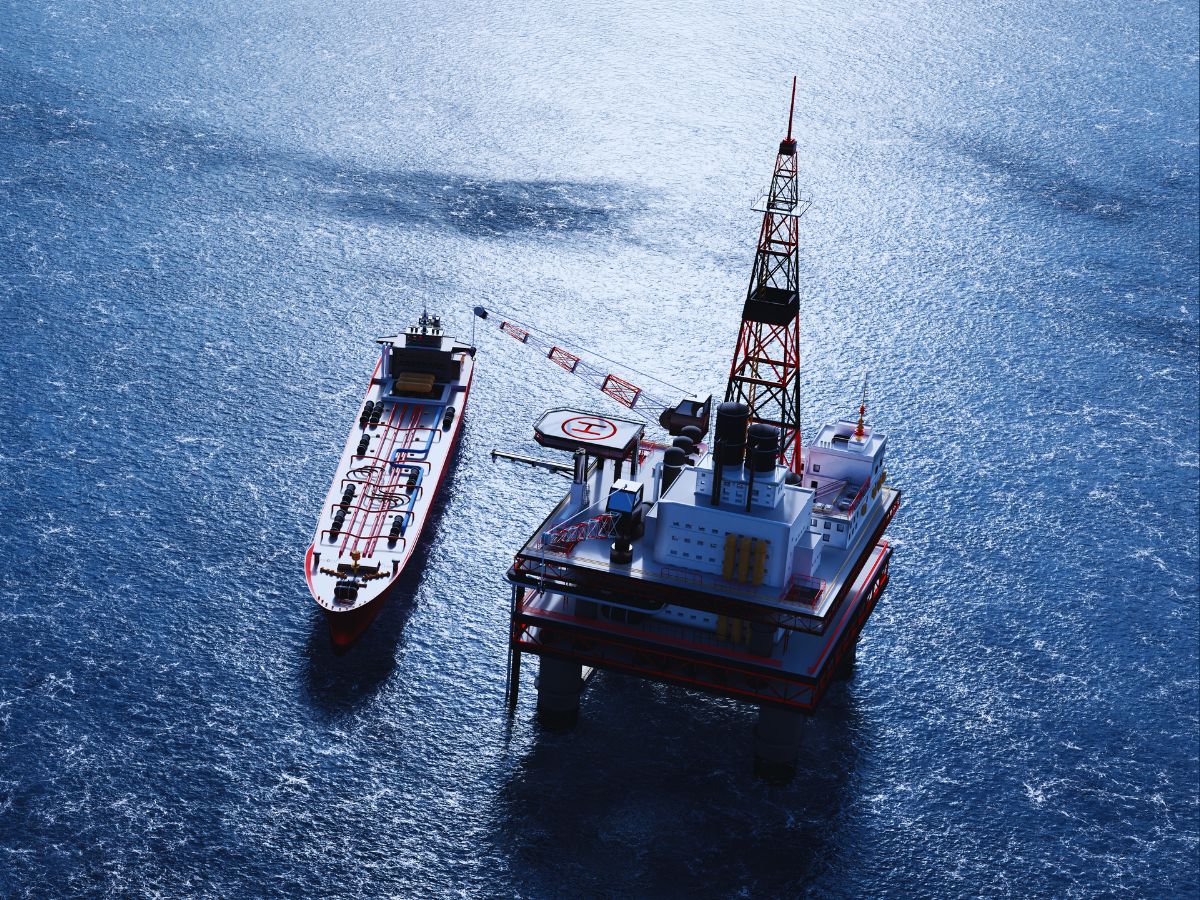
Accurate motion sensors to counter waves effects
Inertial systems are crucial in Active Heave Compensation (AHC) for marine operations. They enhance the stability and precision of equipment in dynamic marine environments.
AHC systems rely on real-time data about the vessel’s movement to counteract the effects of wave-induced heave and ensure smooth and safe operations. Inertial systems, particularly Inertial Measurement Units (IMUs) and Inertial Navigation Systems (INS), provide this vital data by measuring and analyzing the vessel’s motion.
For instance, in crane operations, inertial systems enable the crane to adjust its position automatically, preventing dangerous swings and ensuring safe handling of loads during heavy seas.
Tell us about your projectOur solutions for active heave compensation
Our inertial solutions are designed to enhance operational efficiency and precision in dynamic marine environments. Our advanced motion sensors deliver real-time, accurate data to counteract movement caused by waves and ocean swells. By integrating high-performance inertial measurement units (IMUs) and state-of-the-art algorithms, we provide seamless movements compensation, ensuring smooth operations even in challenging conditions.
Geospatial applications brochure
Get our brochure delivered straight to your inbox!
Do you have questions?
Welcome to our FAQ section! Here, you’ll find answers to the most common questions about the applications we showcase. If you don’t find what you’re looking for, feel free to contact us directly!
What is the difference between active and passive heave compensation?
Active heave compensation (AHC) and passive heave compensation (PHC) are both methods used to mitigate the motion of vessels caused by waves, but they operate in fundamentally different ways:
Passive heave compensation (PHC)
- Mechanism: relies on mechanical or hydraulic systems such as springs, dampers, or accumulators to absorb and counteract the motion of the vessel.
- Energy Source: does not require external power; it uses the natural motion of the system and the forces acting on it to adjust.
- Control: non-adaptive, the system’s performance is based on pre-set parameters and cannot dynamically adjust to changing sea conditions.
- Applications: best suited for steady, predictable environments or operations where precise motion control is less critical.
Active heave compensation (AHC)
- Mechanism: uses motors, hydraulics, or other powered actuators controlled by real-time sensors and algorithms to counteract the vessel’s motion actively.
- Energy Source: requires external power to drive actuators and control systems.
- Control: adaptive, real-time feedback from sensors enables precise adjustments to compensate for dynamic sea conditions.
- Applications: ideal for operations requiring high precision, such as subsea construction, well intervention, or scientific research.
AHC is ideal for applications requiring precise control and active correction of vessel motion, while PHC offers a simpler, more cost-effective solution for operations where precision is less critical and passive absorption of motion is sufficient.
What is AHC in offshore cranes?
Active Heave Compensation (AHC) in cranes is a technology used to counteract a vessel’s vertical motion caused by waves. It ensures that loads lifted or lowered by the crane remain stable and unaffected by the sea’s movement.
AHC systems are particularly critical in offshore operations, where cranes are often used to lift and lower heavy equipment, cargo, or subsea devices from vessels or platforms in dynamic sea conditions. These systems use sensors (such as accelerometers, gyroscopes, or motion reference units) to measure the vessel’s heave (vertical movement) caused by wave action.
Based on this real-time data, the crane’s AHC system automatically adjusts the winch or hoisting mechanism to counteract the heave, ensuring that the load stays at a constant position relative to the seabed or a fixed reference point. Offshore cranes typically use hydraulic or electric systems to make these precise adjustments. The crane’s winch or hoist is rapidly adjusted to lift or lower the load in sync with the vessel’s motion, effectively “canceling out” the vertical motion caused by the waves.
By stabilizing the load during lifting or lowering operations, AHC minimizes the risk of accidents, load swinging, or equipment damage. It allows for safer, more precise operations, especially during the placement of subsea structures or when handling delicate equipment.