Ellipse used in autonomous vehicles navigation
GNSS/INS with dual antenna for navigation and positioning in UNMANNED SOLUTION’s autonomous platforms
” We need ultra-high precision. Because the vehicle is driving on the road, we usually need centimeter-level accuracy. The accuracy of the IMU is very important because the vehicle sometimes loses its GPS signal, such as an environment like a tunnel. ” – UNMANNED SOLUTION R&D Team
UNMANNED SOLUTION, a South-Korean company based in Seoul, is dedicated to the development of autonomous vehicles of all kinds. They develop numerous different projects and activities, such as driverless shuttles, autonomous agricultural equipment, robots, and educational platforms.
The first agricultural tractor integrating an auto guidance system in south Korea
Among these projects is a self-driving tractor. UNMANNED SOLUTION is a pioneer in the modernization of agricultural equipment in South Korea. The company developed an Auto-Guidance System and a self-driving algorithm suitable for the Korean agricultural market and environment.
The Auto Guidance System is a system composed of several components: a GPS/GNSS module providing highly precise positioning, an auto steering module for steering control, and a control console for path creation and tasks settings. The system provides and controls position, attitude and speed data, which are critical information for the tractor to follow the desired path.
Miniature RTK GNSS/INS solution for unmanned navigation
SBG Systems’ Ellipse-D INS (Inertial Navigation System) is integrated into the GPS/GNSS or navigation module as a positioning unit. The inertial sensor is also needed to navigate to the field as well as for a potential wooded area leading to the field. Its role in the GPS Module is, in addition to delivering positioning data, to provide roll/pitch, and heading.
That is to say, the tractor’s 3D position in order to monitor and adjust it if needed.
The Ellipse-D sensor is a dual-antenna RTK GNSS/INS that perfectly meets the application’s accuracy needs, especially in terms of heading. Such applications involving slow vehicles require a highly precise heading because of its low dynamics.
A dual-antenna inertial system delivers more accurate heading than a single antenna solution, even in a stationary position and is therefore recommended for autonomous vehicles with low dynamics.
UNMANNED SOLUTION’s self-driving tractor also integrates a low-level controller, a user interface module, a vehicle control module, and a path-generation and following system.

A wide range of self-driving vehicles for different kinds of applications
Continuing with agricultural equipment, UNMANNED SOLUTION is also developing a driverless pesticide applicator (still under development) designed to fit atypical environments. It is also equipped with an intelligent and automatic pesticide control.
However, the company does not limit its offer to agricultural equipment but to all kinds of autonomous platforms:
- The WITH:US autonomous shuttle. It can operate as an on-demand public transportation service in smart cities. It embeds Velodyne LiDARs, SBG Systems Ellipse-D RTK INS/GNSS, several cameras and controllers, enabling the shuttle to analyze its surroundings and determinate the best behavior to adopt. The shuttle serves for short-distance trips such as campuses, industrial, airport, and downtown areas.
- The WITH:US LOGI autonomous logistics robot used for short-distance deliveries both indoors and outdoors. In addition to being able to access areas where an automobile can’t reach, it also allows customers to choose their preferred date, time and location for delivery. It integrates LiDARs, GPS/GNSS, INS, cameras and controllers like the WITH US Shuttle.
- The WITH:US CARO. This autonomous vehicle has been designed for long-distance and large deliveries, as it can load up to 1,500kg and has a large loading space. It is equipped with the same components as the autonomous shuttle and logistics robot.
- The WITH:US SECURITY robot. As its name implies, it is a self-driving security robot used in short-distance sections of different kinds of environments. It is also equipped with a LiDAR, INS/GNSS, Cameras etc. but integrates an obstacle recognition technology for outdoors applications. It can serve as a patrolling robot.
All UNMANNED SOLUTION’s platforms are equipped with either SBG Systems Ellipse or Ekinox grade RTK GNSS/INS, depending on the application’s performance and accuracy needs.
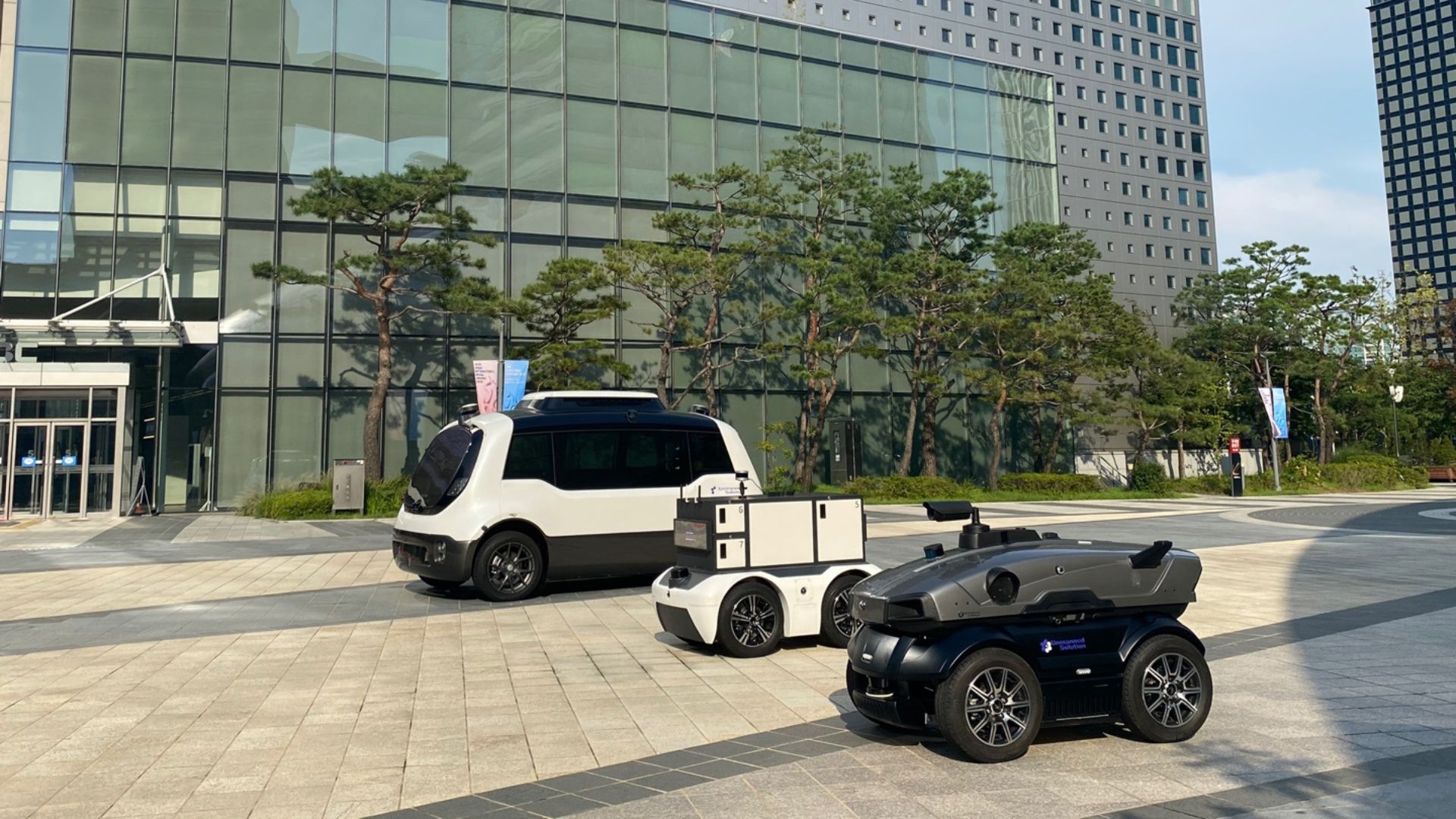
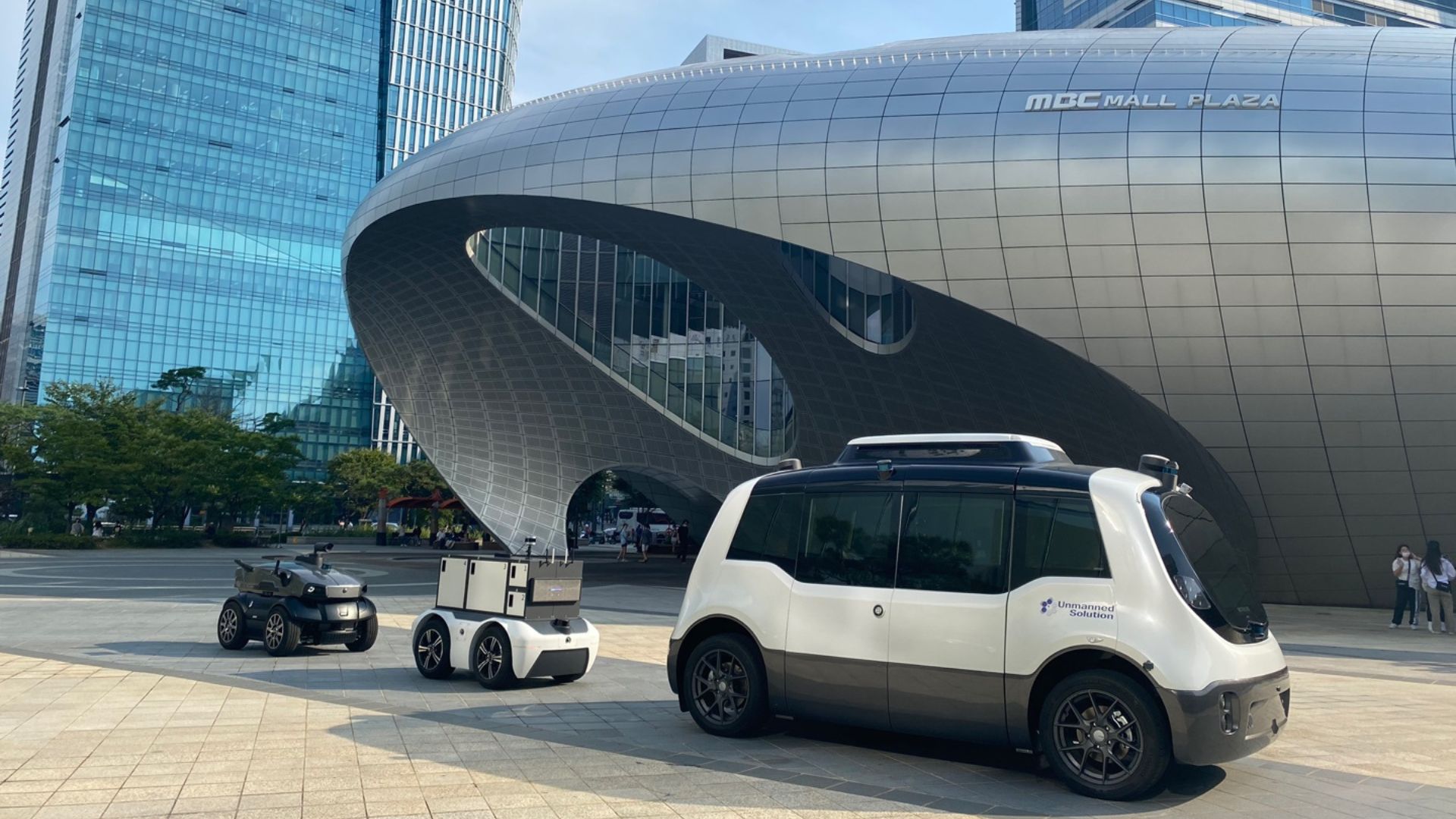
Ellipse-D
The Ellipse-D is an inertial navigation system integrating a dual antenna and dual frequency RTK GNSS that is compatible with our Post-Processing software Qinertia.
Designed for robotic and geospatial applications, it can fuse Odometer input with Pulse or CAN OBDII for enhanced dead-reckoning accuracy.
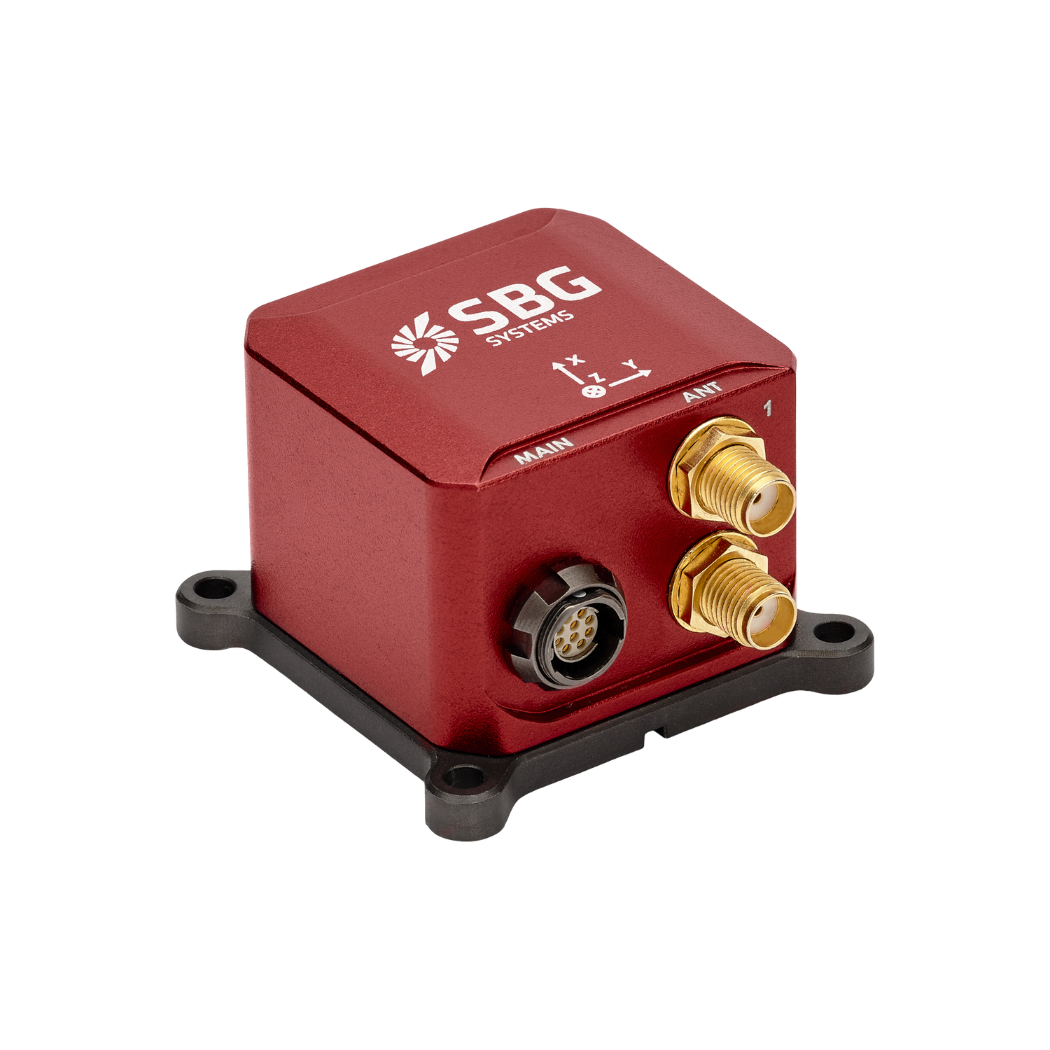
Ask a quotation for Ellipse-D
Do you have questions?
Welcome to our FAQ section! Here, you’ll find answers to the most frequent questions about the applications we highlight. If you don’t find what you’re looking for, feel free to contact us directly!
What is GNSS vs GPS?
GNSS stands for Global Navigation Satellite System and GPS for Global Positioning System. These terms are often used interchangeably, but they refer to different concepts within satellite-based navigation systems.
GNSS is a collective term for all satellite navigation systems, while GPS refers specifically to the U.S. system. It includes multiple systems that provide more comprehensive global coverage, while GPS is just one of those systems.
You get improved accuracy and reliability with GNSS, by integrating data from multiple systems, whereas GPS alone might have limitations depending on satellite availability and environmental conditions.
What is GNSS post-processing?
GNSS post-processing, or PPK, is an approach where the raw GNSS data measurements logged on a GNSS receiver are processed after the data acquisition activity. They can be combined with other sources of GNSS measurements to provide the most complete and accurate kinematic trajectory for that GNSS receiver, even in the most challenging environments.
These other sources can be local GNSS base station at or near the data acquisition project, or existing continuously operating reference stations (CORS) typically offered by governmental agencies and/or commercial CORS network providers.
A Post-Processing Kinematic (PPK) software can make use of freely available GNSS satellite orbit and clock information, to help further improve the accuracy. PPK allow for precise determination of a local GNSS base station’s location in an absolute global coordinate reference frame datum, which is used.
PPK software can also support complex transformations between different coordinate reference frames in support of engineering projects.
In other words, it gives access to corrections, enhances the project’s accuracy, and can even repair data losses or errors during the survey or installation after the mission.
What are the autonomy levels of autonomous vehicles?
The autonomy levels of autonomous vehicles are classified into six levels (Level 0 to Level 5) by the Society of Automotive Engineers (SAE), defining the extent of automation in vehicle operation. Here’s a breakdown:
- Level 0: No Automation – The human driver fully controls the vehicle at all times, with only passive systems like alerts and warnings.
- Level 1: Driver Assistance – The vehicle can assist with either steering or acceleration/deceleration, but the human driver must remain in control and monitor the environment (e.g., adaptive cruise control).
- Level 2: Partial Automation – The vehicle can control both steering and acceleration/deceleration simultaneously, but the driver must remain engaged and ready to take over at any moment (e.g., Tesla’s Autopilot, GM’s Super Cruise).
- Level 3: Conditional Automation – The vehicle can handle all aspects of driving in certain conditions, but the human driver must be ready to intervene when requested by the system (e.g., highway driving). The driver doesn’t need to actively monitor but must remain alert.
- Level 4: High Automation – The vehicle can perform all driving tasks autonomously within specific conditions or environments (like urban areas or highways) without human intervention. However, in other environments or under special circumstances, a human may need to drive.
- Level 5: Full Automation- The vehicle is fully autonomous and can handle all driving tasks in all conditions without any human intervention. There is no need for a driver, and the vehicle can operate anywhere, under any conditions.
These levels help define the evolution of autonomous vehicle technology, from basic driver assistance to full autonomy.
What is georeferencing in autonomous construction systems?
Georeferencing in autonomous construction systems refers to the process of aligning construction data, such as maps, models, or sensor measurements, with real-world geographic coordinates. This ensures that all data collected or generated by autonomous machines, such as drones, robots, or heavy equipment, is accurately positioned in a global coordinate system, like latitude, longitude, and elevation.
In the context of autonomous construction, georeferencing is critical for ensuring that machinery operates with precision across large construction sites. It allows for the accurate placement of structures, materials, and equipment by using satellite-based positioning technologies, such as GNSS (Global Navigation Satellite Systems), to tie the project to a real-world location.
Georeferencing enables tasks like excavation, grading, or material deposition to be automated and precisely controlled, improving efficiency, reducing errors, and ensuring that construction follows design specifications. It also facilitates progress tracking, quality control, and integration with Geographic Information Systems (GIS) and Building Information Modeling (BIM) for enhanced project management.