Vibrations can introduce unwanted noise or distortions into the measurements because MEMS sensors are highly sensitive to external forces. The effects include:
- Cross-axis sensitivity: Vibrations along one axis can be misinterpreted as motion on another axis.
- Resonance amplification: At specific frequencies (sensor’s natural resonance), vibrations can amplify the deflections, leading to erroneous outputs.
- Bias instability: They can cause temporary or long-term shifts in the sensor’s bias (zero-point offset).
- Mechanical fatigue: Prolonged vibrations can wear out or degrade the microscopic structures over time, reducing reliability.
SBG design against vibrations
SBG Systems has designed inertial sensors with a special care on signal processing, using only high quality MEMS sensors, combined with efficient anti-aliasing FIR filters to limit vibration issues. Thanks to the use of low VRE (Vibration Rectification Error) accelerometers, there is no need to do any isolation/damping during installation.
Choosing the right accelerometer option
MEMS technology is highly robust against shocks, but they can be more or less sensitive to vibrations, especially high frequency ones. When buying the sensor, a higher range of accelerometers can be chosen, for example, 16g instead of 8g for Ellipse sensors..
Limit Vibrations around the inertial sensor
Several methods can reduce the impact of vibrations on MEMS sensors:
- Physically damp them with appropriate material, for instance Silent Bloc.
- When dealing with a low weight sensor (for instance Ellipse), it might be necessary to damp the sensor together with a heavier mass (like a battery) to damp vibrations more easily. It is always easier to isolate a heavier system from them.
- Use flexible cables to avoid transmitting them through the cables.
- In case of high frequency, check if they are propagated by the air (sound) and isolate the device accordingly with sound absorbing materials.
SBG factory tests using a shaker
SBG Systems performs various tests on its sensors. Sensors behavior is characterized, so the level and frequency can stand is known, and specifically tuned algorithms can be designed. The test method used is the MIL-STD-810G (defined by the U.S. Department of Defense) minimum integrity figure shown below.
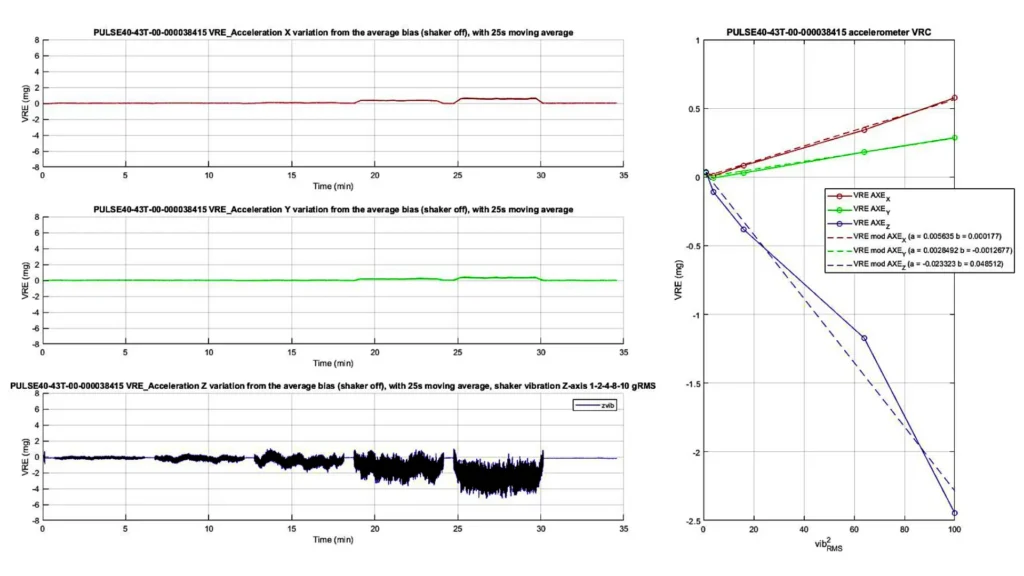